FRP (GRP) Tank
The vessel or tank is designed for the most severe combination of conditions which may vary in every needs.
*It is suggested to consult with the fabricator to meet precise result to suit with the conditions.
Fabricated by contact molding with Filament-Wound and Hand Lay-Up methods.
For more than 24 years PT Teknoglass Duromer Internusa has been fabricating FRP (GRP) industrial equipments for various type and size. Specifically engineering designed to meet specific requirements.
Commonly there are 2 types of FRP (GRP) Tanks such as storage & processing tanks. Both are available to be used for non-chemical or chemical resistance purpose.
All of FRP (GRP) Tanks that been fabricated complied to international standard such as:
FRP Tank |
||
No. | Description | Standard Design Code |
1 | Processing Tank PRESSURE | ASME SECTION X |
2 | STORAGE and Tank pressure | BS 4994 |
3 | ASME BOILER and PRESSURE VESSEL CODE | ASME BPVC |
4 | Contact-Molded Glass-Fiber-Reinforced Thermoset Resin Corrosion-Resistant Tanks | ASTM D4097 |
5 | Standard Specification for Filament-Wound Glass-Fiber-Reinforced for Tank Process | ASTM D2143 |
6 | Standard Specification for Filament-Wound Glass-Fiber-Reinforced Thermoset Resin Corrosion | ASTM D2996 |
7 | Standard Specification for Filament-Wound Glass-Fiber-Reinforced Thermoset Resin Corrosion-Resistant Tank | ASTM D3299 |
8 | Standard Specification for Contact-Molded Glass-Fiber-Reinforced Thermoset Resin Corrosion-Resistant Tanks | ASTM D4097 |
9 | Storage or Processing Tank at pressures not exceeding 15 psig external and/or internal above any hydrostatic head | ASME RTP-1 |
10 | Standard Specification for Contact-Molded Reinforced Thermosetting Plastic (RTP) Laminates for Corrosion-Resistant Equipment | ASTM C522-9 |
Design comes with isometric (2D) drawings and 3D model which are more easy to be read.


Maximum size & dimension of production capability are limited by inland transportation. Maximum dimension for inland transportation: L 12.000mm x H 3800mm.
Products which over the maximum size & dimension for inland transportation will be fabricated on site or could be negotiable.
Industries Served:
Chemical Plant, Waste Water Treatment, Oil & Gas Industry, Pulp & Paper Industry, Wind Farm, Transportation Industry, and many more.
Potential Uses of FRP (GRP) In Industrial Sector:
Drill Sites – Mud Handling Equipment, Offshore Platforms, Field Liquid Storage Vessels (Chemical / Non- Chemical), Brine and Saltwater Lines, Saline/Brine Discharge Lines, Undersea Gathering Lines, Pipe Linings, Casing Linings, New Pipelines, Railway Tank Cars, Etc.




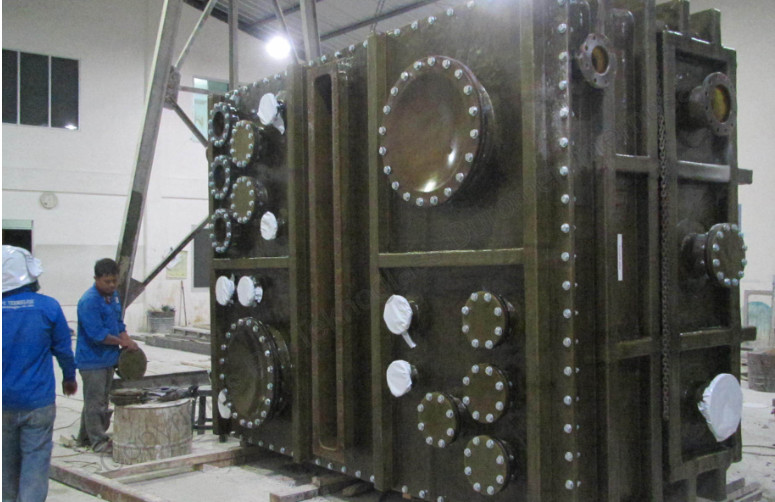
GALLERY
View more images of FRP (GRP) Tank
COMPARISON OF FRP (GRP) AND OTHER MATERIALS
Read about characteristics of FRP (GRP) material among other materials
GENERAL TYPES, DIMENSION & SPECIFICATION
HORIZONTAL STORAGE TANK TYPE CYLINDER with DISH DOME / FLAT END CAP |
- ISOMETRIC VIEW
- REAR VIEW
- SIDE VIEW
- FLAT
- DOME
FRP RECTANGULAR TANK |
- ISOMETRIC VIEW
- TOP VIEW
- FRONT VIEW
- SIDE VIEW
FRP SQUARE BATH |
FRP STORAGE TANK (Cone Cover & Cone Bottom) |
- ISOMETRIC VIEW
- SIDE VIEW
- TOP VIEW
Vertical Process Tank Type Cylinder, Flat Cover and Dish Dome Bottom |
- TOP VIEW
- SIDE VIEW
- ISOMETRIC VIEW
Vertical Process Tank Type Cylinder, Flat Cover and Cone Bottom |
- SIDE VIEW
- ISOMETRIC VIEW
- TOP VIEW
Vertical Storage Tank Type Cylinder, Flat Cover and Fal Bottom |
- TOP VIEW
- SIDE VIEW
- ISOMETRIC VIEW
Cyclone Vertical Tank Type Cylinder, Dish dome Cover and Cone Bottom |
- TOP VIEW
- SIDE VIEW
- ISOMETRIC VIEW
FRP Scrubber Tank Type Cylinder, Flat Cover and Flat Sloop Bottom |
- TOP VIEW
- SIDE VIEW
- ISOMETRIC VIEW
Vertical Storage Tank Type Cylinder Dish Dome Cover and Cone Bottom |
- ISOMETRIC VIEW
- TOP VIEW
- SIDE VIEW
Support Tank Concrete for Vertical Tank Cone Bottom |
- ISOMETRIC 3D
- TOP VIEW
- ISOMETRIC 3D
- SIDE VIEW
Support Tank Type Leg for Vertical Tank Dish-Dome Bottom |
- SIDE VIEW
- TOP VIEW
- ISOMETRIC VIEW
- SIDE VIEW
- ISOMETRIC VIEW
Support Tank Type Leg for Vertical Tank with Cone Bottom |
- TOP VIEW
- SIDE VIEW
- ISOMETRIC VIEW
- ISOMETRIC VIEW
Support Tank Type Leg for Cone Bottom |
- TOP VIEW
- SIDE VIEW
- ISOMETRIC VIEW
- ISOMETRIC VIEW
Vertical Support Tank Type Leg for Cone Bottom |
- SIDE VIEW
- TOP VIEW
- FRONT VIEW 3D
- ISOMETRIC VIEW 3D
Standard Minimum Thickness for Horizontal Tank Contact Moulding |
Design Pressure : ATM
STANDARD CODE : ASTM D3299 and ASME RTP-1
Fabrication Method : FILLAMENT WOUND FOR SHELL
Note:
Thickness may vary on every needs. Depend on tank’s conditions, situations, and designs. Table shown for reference purpose only. It is suggested to consult with the manufacturer to meet precise result to suit your needs.
Standard Minimum Thickness for Vertical Tank Contact Moulding |
Design Pressure : ATM
STANDARD CODE : ASTM D3299 and ASME RTP-1
Fabrication Method : FILLAMENT WOUND FOR SHELL
Note :
ASME RTP-1 The Minimum thickness of Flat Bottom :
?0.27 in. for inside diameter <72 in.
?0.31 in. for inside diameter >72 in. to <96 in.
?0.4 in. for inside diameter >96in. to <144 in.
?Thickness may vary on every needs. Depend on tank’s conditions, situations, and designs. Table shown for reference purpose only. It is suggested to consult with the manufacturer to meet precise result to suit your needs.
This site is protected by reCAPTCHA and the Google Privacy Policy and Terms of Service apply.